Metal Forming Dies and Tooling
At Innovative Carbide, we have decades of experience and expertise in delivering dies and tooling that perform to the highest quality in rigorous metal forming environments. Our proven superior impact grades (IC-320 and IC-325) can withstand any metal forming process.
We round out our cold heading tool belt with IC-13, IC-15, and IC-311, providing higher wear impact grades for improved performance.
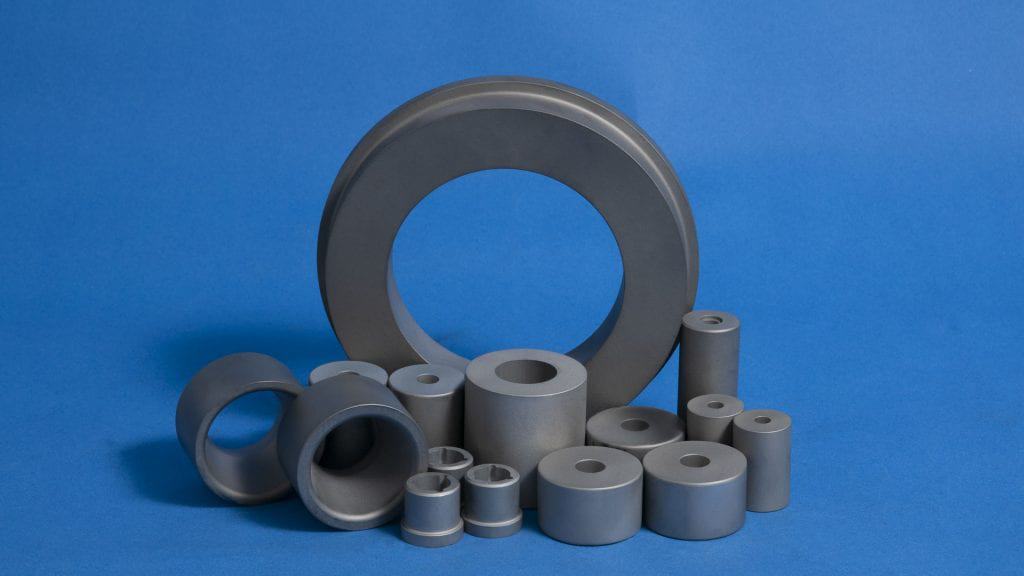
Common Metal Forming Dies Applications
With almost endless applications, our metal forming dies support a range of industries. We are a metal-forming industry leader and provide only the highest-quality tungsten carbide forming dies. Innovative Carbide provides tungsten carbide dies suitable for everything from bending and rolling to extruding and shaving.
- Saw Blades
- Slitting Knives
- Shear Knives
- Circular Knives
- Rotary Knives
- Seal Rings
- Reduction Dies
- Compacting Dies
- Draw Dies
- Wire Dies
- Forming dies
- Extrusion Dies
- Stamping Dies
- Blanking Dies
- Header Dies
- Swaging Dies
- Cold Heading Dies
- Rectangular Blanks
- Rods
- Punches
Different Grades of Tungsten Carbide We Offer
Innovative Carbide knows that every tungsten carbide application is unique. We offer a wide range of superior quality proprietary grades to meet your specific needs.
Using a thorough and exacting process for manufacturing our tungsten carbide grades, we pay strict attention to detail. This ensures excellence from conception to the final product.
We guarantee the highest material quality and consistency of our products. We do this with our ISO 9001:2015 Certification manufacturing process so that our customers get the industry’s best quality carbide available.
Our Dedication to Quality
Innovative Carbide uses a unique no-wax process to improve the carbide die manufacturing process. By eliminating the need for adding wax powder to the carbide powder, we can reduce issues like carbon control problems, porosity, shrinkage, and improve consistency and cost savings when grinding.
Traditional approaches use wax and binders to improve the strength of the powder compact.
With our process, we prevent issues like:
- Carbon control or “free-carbon” that could lead to cracking and chipping
- Increased porosity that weakens the final product
- Distortions and size/dimension variation problems
Our Services
As your partner, Innovative Carbide provides reliable cost-effective solutions to your most demanding wear applications.
- Low and high-volume part production
- Prototype work
- Semi-finished parts
- Metallurgical inspection and services
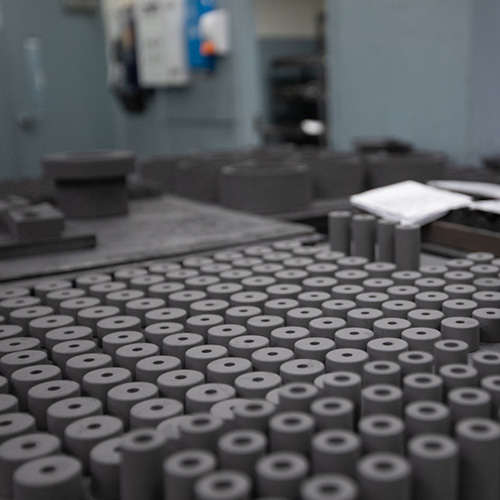
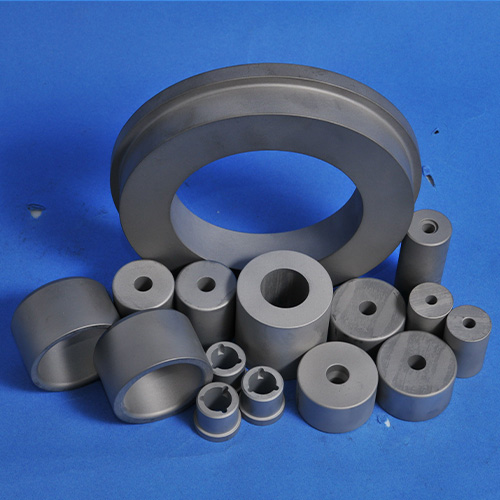
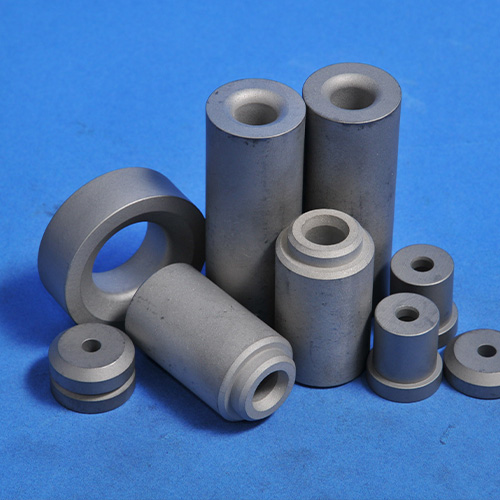

To discuss your metal forming dies needs with a process expert, contact Innovative Carbide today.